Master Standard Operating Procedure
1. Vehicle Drop Off
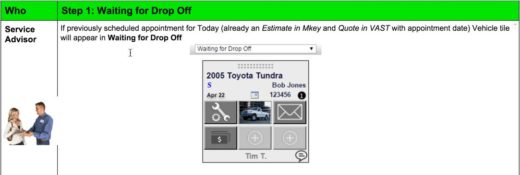
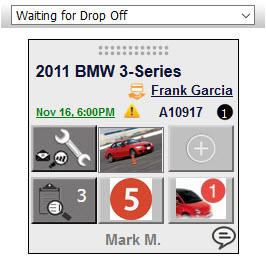
On SmartFlow
Appointments for that day in POS show up in this column
Service Advisor Basic Actions
SA uses Drop Off Script to collect the email address and enters it into the PoS.
The email address is obtained.
SA creates initial work order
There must be at least one job(labor line) on the work order to allow technician assignment.
- Service Advisor converts estimate/quote to a workorder if an already existing appointment.
- Service Advisor writes workorder if no appointment exists.
- Service Advisor makes the first job on the workorder the inspection.
SA orders parts using POS
Service Advisor Advanced Actions
SA uses Drop Off Script to collect the email address and enters it into the PoS.
The email address is obtained.
SA creates initial work order
There must be at least one job(labor line) on the work order to allow technician assignment.
- Service Advisor converts estimate/quote to a workorder if an already existing appointment.
- Service Advisor writes workorder if no appointment exists.
- Service Advisor makes the first job on the workorder the inspection.
SA orders parts using POS
Technician Actions
Owner Oversight
Best Practices For Drop Off Step
(3.1.6) Uses Drop Off script |
(3.1.3) Obtains customer’s email addresses |
(3.1.8) Uses 2nd monitor to show inspection and images at the counter and educating motorist |
Reports Used For Drop Off Step
2. Initial Work / Inspection
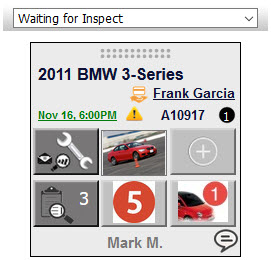
On SmartFlow
When appointment is converted to a workorder in POS it automatically shows up in this step.
Service Advisor Basic Actions
SA assigns vehicle to technician(s) or
- SA moves vehicle to Tech column
- SA confirms jobs are authorized on pop up window
- The assignment depends on available hours for the techs. The tech view shows remaining hours available and thus the combination of remaining hours, skill set needed, vehicles about to be finished and promised date/time allows the SA to determine the next technician.
SA Continues working while Technician performs inspection
SA receives audible and visual alert on TVP when inspection is complete
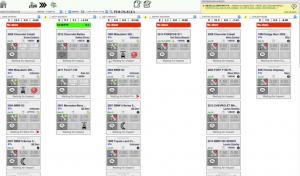
SA moves the vehicle tile from Waiting on Inspect to Waiting on Estimate
- This step is critical to ensure that the new jobs added to the workorder will NOT show up on the Technicians tablet as “Approved”
SA Advanced Actions
SA/Technician Foreman assigns vehicle to technician(s) or
- Technician moves vehicle to their own named column
- The assignment depends on available hours for the techs. The tech view shows remaining hours available and thus the combination of remaining hours, skill set needed, vehicles about to be finished and promised date/time allows the SA to determine the next technician.
SA uses chat feature to communicate additional info
- parts location
- special instructions not on the work order
SA monitors smart alert messages, automated inspection progress messages or other tech alerts and responds swiftly, e.g.,
- get/order a part, when needed
- get information needed back to tech
SA receives audible and visual alert on TVP
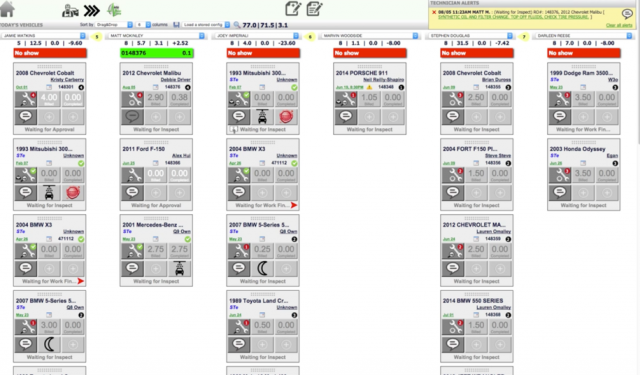
SA moves the vehicle tile from Waiting on Inspect to Waiting on Estimate
- This step is critical to ensure that the new jobs added to the workorder will NOT show up on the Technicians tablet as “Approved”
Technician Basic Actions
Technician hears Audible Alert
Technician reviews workorder
Tech performs inspection
- Take the tablet to the vehicle and perform inspection according to the inspection procedure
- Follow picture policy
Technician submits Digital Inspection once complete
Technician Advanced Actions
Technician hears Audible Alert
Technician reviews workorder
Technician conducts walk around portion of inspection
- Verify vehicle information
- VIN – Scan vin if new customer and there is no VIN on the workorder.
- License Plate – Enter the correct license plate number.
- Mileage – Enter vehicle mileage when workorder promts you.
- Take a profile photo of the vehicle to replace the stock photo.
- Take photos of all 4 corners from approximately 5 feet away to capture vehicle body condition. Note: most body damage is captured in these 4 pictures and multiple scratch and dent photos are not necessary.
- Take photo of state inspection sticker
- Take photo of vin/tire placards in door opening
- Start vehicle and take photo of instrument cluster with engine running and all systems initialized. This captures any warning lights that may be on before service, mileage, and fuel state.
Tech performs inspection
- Take the tablet to the vehicle and perform inspection according to order on the sheet
- Open vehicle and perform road test first
- Send chat to SA about leaving for road test
- Select conditions and actions for every item not “Good”
- Follow picture policy
- Uses speech to text to document additional notes back to the service advisor
- Uses circle to mark special areas for the SA to educate the motorist about
- Uses ‘zzz’ to separate the info for the SA only from the info for both the motorist and SA
Technician submits Digital Inspection once complete
Tech performs jobs on work order and marks completion accordingly
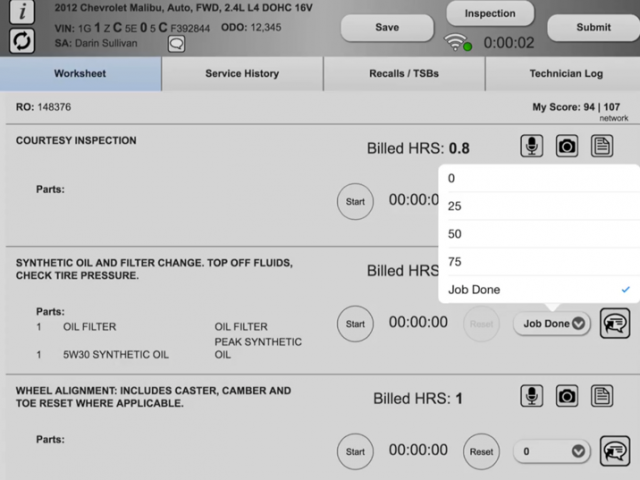
Tech uses chat and Smart Alerts
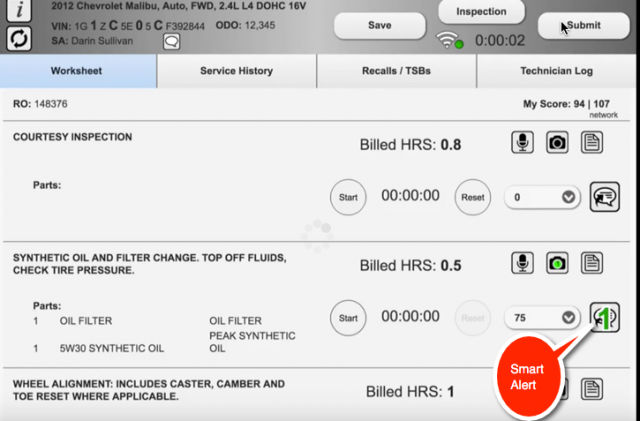
Owner Oversight
Daily oversight of the inspection process is important to ensure that the new procedures are being conducted so that the the Service Advisor and Motorist can benefit from a proper inspection
Best Practices For Inspect Step
(3.1 .4) Picture policy is followed |
(3.1.2) Technician selects Condition and Action for EVERY topic that is other than “Good” |
(3.1.5) Technician highlights problem area when taking pictures |
Inspection Metrics Report is used to verify Picture Policy is enforced and Technicians are recommending actions on the inspection sheet
The Technician Effectiveness Report is used to monitor for over/under recommending and pencil whipping of the inspection process.
Avg. total time [h] / inspection – the duration is the total time the car is on the workflow step “inspect” (so it’s dependent on the SA moving it to the other workflow steps)
3. Waiting for Estimate
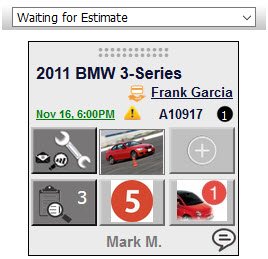
On SmartFlow
SA Actions
SA reviews the inspection results
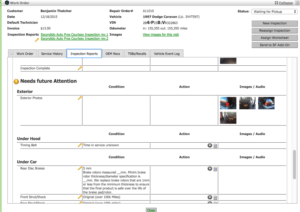
- Check report for picture policy compliance. Ensure all required pictures have been taken
- Edit photos using red circle and arrow to guide motorist to problem area
- Verify all “conditions” are matched with “actions” from canned jobs and are appropriate, edit where needed
- Verify all grammar and notes are appropriate for motorist review, edit where needed
- Verify that statuses(good, future, immediate) are correct for the condition, edit where needed
- Edit any remaining items on inspection report
- Add OEM recommendations to report/workorder
SA emails inspection report to motorist
- Click on “email” button and customize the message as needed prior to sending.
SA builds estimate in POS
- SA adds all recommended actions from the inspection to the estimate/work order using the “EST” button on the SmartFlow add on
- SA adjusts labor times as necessary if canned job is different than actual required labor time
- SA adds parts and pricing
- SA makes sure all recommended actions have a line item on the estimate
- SA prioritizes jobs on estimate so it follows priority on inspection report
SA moves vehicle to Waiting for Approval
Technician Actions
Technician continues working
- Tech keeps workorder open at all times for any vehicle that he is working on
- Tech reactivates vehicle from the IDLE screen, if further work can be performed before the authorization has been finished
- Tech uses job timer for time and material work and marks the jobs complete
- Tech updates job completion status as jobs are complete or prior to “saving” or “submitting” any workorder
Owner Oversight
- Every recommended action is imported into the workorder/estimate. Every item other than “good” on the inspection report should have a line item on the estimate
- Average pictures per inspection is above the number in the picture policy
- 100% of inspections manually emailed to customer
Best Practices For Estimate Step
Service Advisor reviews every inspection for:
|
(3.1.8) Uses Dual Screen
Screen 1: SMS Screen Screen 2: SmartFlow/ Inspection Screen |
(3.1.9) Image editor for service advisor (10%-20% of completed inspections should have an edited image) |
(3.1.3) Inspections are emailed to the motorist, manually and automatically at pick up |
(3.1.12) 100% Recommended actions are converted to jobs on estimate |
4. Waiting on Approval
SA adds jobs coming from the inspection to the work order in order to estimate the new work order value and get it authorized by the motorist
SA marks declined jobs as such and makes sure they will be included in the service recommendation at vehicle pick up and later in the service reminder.
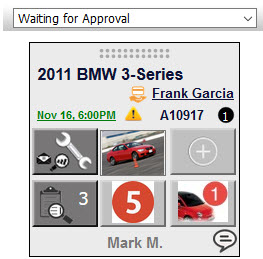
On SmartFlow
SA contacts customer and uses inspection report to sell work.
SA Actions
SA calls motorist to review inspection and gain approval
SA brings up motorists inspection results PDF before calling by following the two steps below:
- Click on customer name
- Click on Create PDF
SA calls motorist and goes through inspection results and educates on the needed work
- SA askes customer if they have reveiwed the inspection report
- SA asks customer to open the inspection report on their smartphone or computer
- SA has same report open on their workstation
- SA consults customer about inspection report items
- SA mentions good things and points out that it pays to maintain your vehicle
- SA covers future attention items
- SA covers immediate attention items
- SA show pictures to the customer of good and attention items and relies on edited photos to point out problem areas
- SA answers remaining questions on inspection report
- SA asks “can we get started on this today”
- SA answers price questions only after reviewing the report with motorist and educating them
SA Declines jobs not approved by motorist
SA moves vehicle tile to Waiting on Work Finished or Waiting on Parts on the TVP
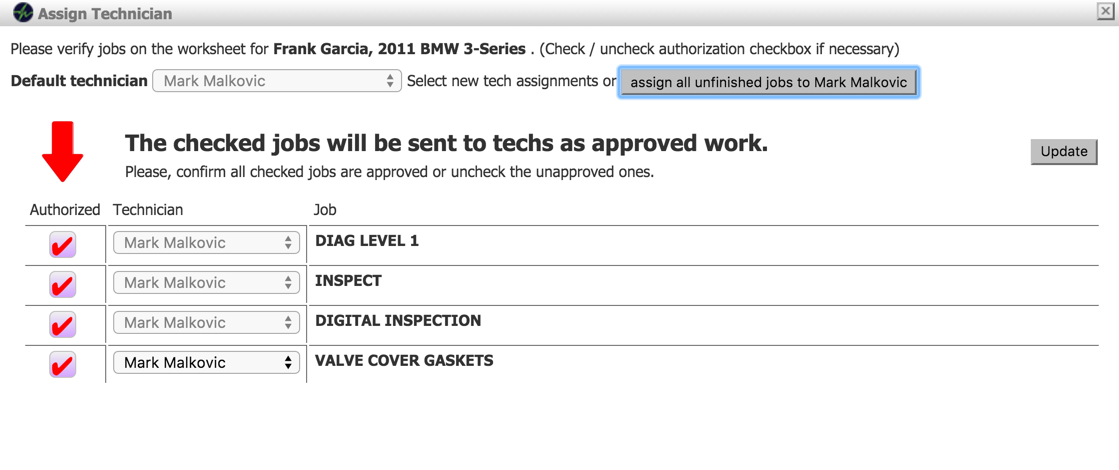
Technician Actions
Technician continues working
- Tech keeps workorder open at all times for any vehicle that he is working on
- Tech reactivates vehicle from the IDLE screen, if further work can be performed before the authorization has been finished
- Tech uses job timer for time and material work and marks the jobs complete
- Tech updates job completion status as jobs are complete or prior to “saving” or “submitting” any workorder
Owner Oversight
Best Practices For Approval Step
(3.1.8) Uses 2nd monitor to show images at the counter and educating motorist |
(3.1.7) Talking motorists through the inspection results showing good areas and bad areas |
[/learn_more]
5. Waiting on Parts
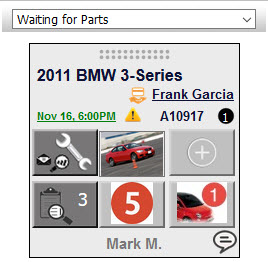
On SmartFlow
Communicate ETA’s with Technicians via chat.
SA Actions
SA orders parts using POS
SA communicates parts ETA to Technician
SA informs Technician of parts arrival
SA moves vehicle tile to Waiting on Work Finished on the TVP
Technician Actions
Technician continues working on vehicles as assigned
Technician responds to chats about parts status
Owner Oversight
6. Waiting for Work Finished
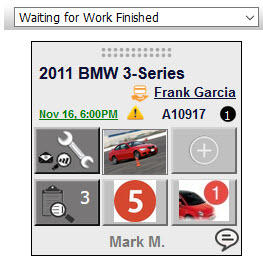
On SmartFlow
Monitor for alerts and job progress indications.
SA Actions
SA chats to Technician any special notes
- Promise time changes
- Requesting updates to job completion status
- Info on any additional parts requested
SA responds to alerts and chats in timely manner
Technician Basic Actions
Technician receives audible alert
Technician opens workorder
Technician performs jobs on workorder
Technician submits completed workorder
Technician Advanced Actions
Technician receives audible alert
Technician opens workorder
Technician starts job timer (for time and material work)
Technician uses chat and Smart Alerts
Technician updates workorder comments
Technician marks jobs complete
- A job is complete
- Selecting “Save” on the workorder
- Selecting “Submit” on the workorder
- When requested by the SA
Technician submits completed workorder
Owner Oversight
Best Practices For Work Step
(3.1.20) Tech uses chat to communicate with SA |
(3.1.20)Tech “Keeps it Digital”
|
(3.1.24) Tech opens vehicle on tablet when work starts and leaves vehicle open while working on vehicle. |
(3.1.25) Technician submits workorder when work is done |
(3.1.26) Techs mark off progress of all jobs every time they “save” a workorder and move on to another vehicle.
|
(3.1.26) Techs mark Job done on every jobs at the time of completion. |
(3.1.19) Techs use speech to text to document |
Techs take photos as appropriate on each job line |
(3.1.27) Techs use Smart Alert for instant SA notification
|
(3.1.28) Techs remain in shop area and do not enter SA area for regular operations |
7. Vehicle Pick Up
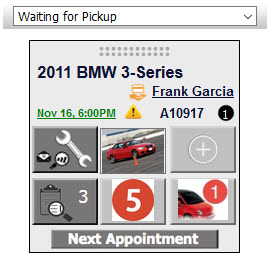
On SmartFlow
Review work with customer and schedule next appointment.
SA Basic Actions
SA receives audible and visual alert on TVP
SA moves vehicle tile to Waiting for Pickup
SA prepares invoice in POS
SA notifies motorist that vehicle is ready for pickup
SA Advanced Actions
SA receives audible and visual alert on TVP
SA verifies all jobs marked complete
SA moves vehicle tile to Waiting for Pickup
SA prepares invoice in POS
- SA reviews workorder on TVP and assigns technicians in POS(if using POS for payroll)
- SA adds comments where necessary in POS
- SA ensures all declined work is saved as a recommendation in POS
- SA verifies final price is what was quoted to motorist
- SA converts workorder to invoice
SA notifies motorist that vehicle is ready for pickup
- On TVP the SA clicks on the customer communication button
- SA selects method of communication agreed upon during drop off and selects canned message for pickup
- SA sends notification message
- SA follows up with phone call to motorist if agreed upon during the drop off process
SA greets customer and reviews invoice in person
- Jobs performed this visit
- Jobs saved for future visits
- Warranty policy for jobs performed this visit
SA Schedules next appointment
Retention customers only: On TVP the SA clicks next appointment and schedules the next appointment to:
- Schedule next regular service appointment based on interval selected
- Schedule follow up appointment for the declined jobs which are now recommended services/repairs
Technician Actions
Technician moves on to next vehicle
Owner Oversight
Best Practices For Pickup Step
(3.1.8) Uses 2nd monitor to show inspection and images at the counter and educating motorist |
Proficiency Exercise For Pickup Step
Reports Used For Pickup Step
- Turbo V5.0.2 and V5.0.3 Features and Benefits - December 30, 2018
- Turbo V5.0.2 Features and Benefits - December 18, 2018
- The Business Control Panel with Bill Connor - December 7, 2018